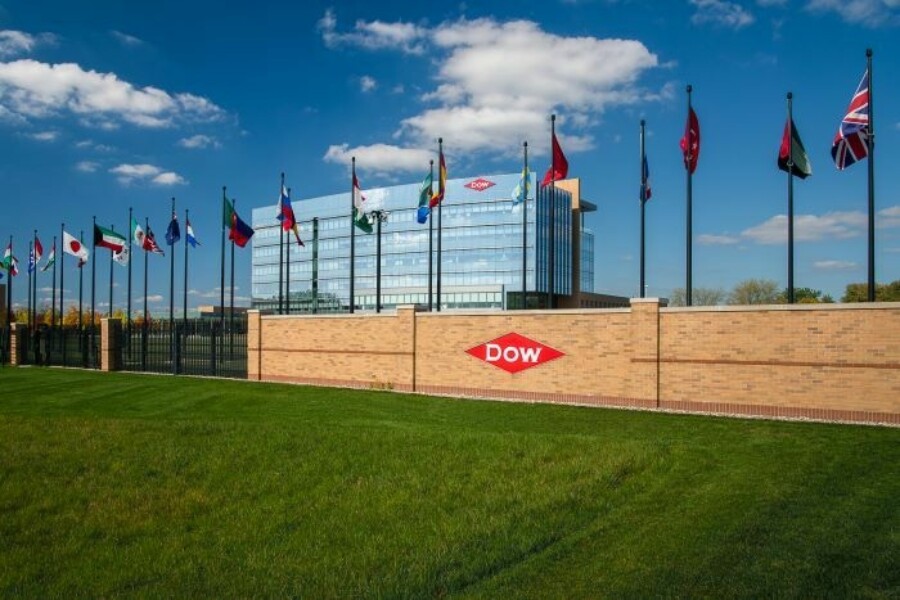
Photo: Dow, Inc.
It’s hard to imagine a bigger or more complex chemical company than Dow, Inc. Starting from humble roots in a small town in central Michigan at the turn of the 20th century, it’s now one of the three largest chemicals producers in the world with 36,500 employees and more than 100 manufacturing sites in 31 countries.
One ERP After Many Mergers and Acquisitions
Even after a series of mega-mergers, spinoffs, and splits—Dow has remained a committed SAP customer. Today, it is enjoying the benefits of the digital transformation work it has been doing dating back to 2012. Using that work as a foundation, the IT leadership at Dow has stayed true to the principle of one global ERP system across all of its business units—SAP ECC. This is a major win, considering that consolidating ERP systems is a tough task for much smaller organizations, let alone a company of Dow’s size.
ASUG spoke with Global IT Director Chris Bruman to hear more about what the business is gaining from its “one global ERP” approach. Chris has spent nearly 30 years at Dow working across various business and IT roles. Because of his experience, he naturally sees the perspectives of both groups and keeps a strong focus on what’s best for Dow’s overall business objectives.
In part one of a two-part series, Chris gave us an overview of some of Dow’s biggest technology initiatives, described the effects of marketplaces like Amazon on the B2B landscape, and shared his perspective both on the business case for SAP S/4HANA and data quality.
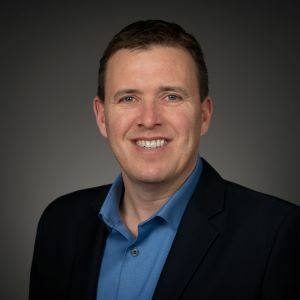
Ann Marie: Tell us a bit about your role at Dow and what you’re responsible for today.
Chris: I have two roles. First, I lead our enterprise systems team, which is responsible for our ERP systems and the ecosystem around them. In other words, the applications and support for many of our company’s processes including supply chain, manufacturing, purchasing, finance, and other areas. Our team owns the projects to improve these systems and services, and we are responsible for driving adoption and offering ongoing support.
I also have a second role as the IT director for one of our six business units—Dow Industrial Solutions—aligned with the business president for that unit. This is a structure we put in place for all six of our business units, where a direct report to the CIO owns the digital strategy for that business and acts as a liaison between business and IT. That business unit is quite complex. Right now, one of the products it is making is isopropyl alcohol, which is, of course, a primary ingredient in hand sanitizer. You can imagine the demand for that.
Ann Marie: You’ve been at Dow for nearly 30 years and have moved through a variety of technology roles. How has that helped you gain perspective on how to implement and support major technology systems like your SAP ERP?
Chris: I’ve spent time both on the project side and the operations side of the business. I’ve also spent two different stints during my career in the purchasing function. This has helped me think beyond the immediate project and more about the long-term impact and the outcome. I think sometimes we can get too close to our projects when we should focus on what is most important for the company.
It can be challenging to prioritize every request that comes in and to focus on what makes the most sense for the company holistically. We need to validate everything to make sure it will bring measurable, tangible impacts, such as driving growth or efficiency and improving the employee experience or the customer experience, for example.
Ann Marie: Could you give me a brief overview of the SAP landscape at Dow?
Chris: We’re on SAP ECC business suite as our core ERP system, on-premise. We implemented that from 2012 to 2014. Now we have one global ERP instance, which is actually quite unusual for a company of our size and complexity. As you can imagine, that gives us a very definitive advantage when it comes to common processes across the company, and most importantly, access to global data in real time with our reporting capabilities through SAP Business Warehouse.
For example, when you’re working with many ERP systems, a simple request to get sales order data can take a long time to complete. For us, it’s a short query into our global reporting system. That real-time data has been an advantage for us.
We also use SAP Concur for travel expenses and SAP Ariba for procure-to-pay automation and catalog buying. We have SAP SuccessFactors as our learning hub. And then lastly, we use Qualtrics to manage our customer experience index dashboard.
Ann Marie: What are some of your most important technology initiatives now?
Chris: We have placed a significant focus on improving our services and our processes related to customer experience and what we broadly call fulfillment. We have programs improving how our customers can digitally place orders, for example, and then see the status of their orders. We’re all after this Amazon-like experience in our industry. That’s a challenge for our industry, but we’re making big strides this year with online order placement and order status updates. We have programs that will improve the processes and tools that we use with Dow customers—for example, pricing management and pricing tools. CRM is a big area of focus for us, along with transportation visibility.
We also have a couple of large programs focused on driving speed and efficiency at our manufacturing sites. There, we’re looking at increased use of digital tools to help us execute large maintenance events and capital projects. At a company like Dow, we could experience a large maintenance event that could cost us millions of dollars. When we can use digital and Internet of Things (IoT) capabilities to remove a few percentage points of cost from those projects, it’s a big deal for our bottom line.
Ann Marie: How have you had to adjust your projects, given the business challenges and conditions that we’re all facing right now?
Chris: One thing I would say has been a surprise was that in the massive shift to work-from-home, our team is delivering really well. We haven’t seen an impact on our program delivery. We’re learning a lot—as is every company—about how remote teams work well and what we can do differently. We’ll carry a lot of what we learned forward once we get back to the office.
Ann Marie: From an IT perspective, were you ready to sort of flip the switch and get everybody remote quickly, or did you have to do anything to prepare for that?
Chris: Our Shanghai team switched in February to work from home. It was like a pilot program, and it worked really well. Then when the pandemic hit the rest of the world and we quickly had to move Europe, North America, and South America to remote work, we had to make a few adjustments with our network collaboration providers. But we made changes quickly and, despite a couple of little issues here and there, overall, it’s been seamless. It’s been a proud moment for our IT team.
Ann Marie: It’s kind of a technology equation plus a culture equation too, isn’t it? The technology has to be there, but then how do you interact with your peers? How do you remain accountable? Those factors are on the cultural side.
Chris: The cultural shift is certainly the harder part. The first few weeks, people were nervous about being isolated and not seeing their teammates. But we’ve adapted. I think people miss the human interaction, but they’ve adapted really well. Like many other companies, we started having regular check-ins with our teams, virtual happy hours, and other ways to keep the team engaged.
Ann Marie: You mentioned that you’re on SAP ECC. What are Dow’s plans regarding SAP S/4HANA and how do those plans fit in with your overall approach to managing your ERP?
Chris: As you know, an ERP program is a massive investment for a company of our size. We’re already working on the strategy and have partnered with SAP over the last 12 months to put together an initial viewpoint on what we call our next-gen ERP strategy.
We’re going to continue on SAP ECC for several more years. Again, we just completed our implementation in 2014. That sounds like a long time, but six years on an ERP implementation isn’t that long. Any shift we make to a new ERP system will be based on a business strategy versus a technical strategy.
I believe one of the biggest factors for us to move to the next generation of ERP will be how and when we can re-engineer our business processes. We have business processes that are 20 to 30 years old and the world has changed since then. As the company rethinks these processes, that will become a catalyst for us to start an ERP program to adopt more-standard processes. Like many companies, we have more customization in our ERP solution than we would like. We would really like to limit any customization to the core and move any specific needs out into the systems of engagement—or “systems of innovation” as we call them. We want to use microsystems instead to deliver the user interfaces with the variations needed across our businesses and keep these functions out of our ERP system as we go forward.
Ann Marie: Honestly, that’s the right reason to do it. If you can use SAP S/4HANA as a catalyst for making other needed changes to the business, that makes for a far more future-looking project.
Chris: Yes, at some point that will happen. But right now, we have support for SAP ECC through 2027. That’s the only hard line we have right now. It’s really challenging to build the value case, from a business standpoint, to do a big ERP swap-out. Everyone wants the newest and the greatest system, but it’s very difficult to put this business case down on paper and justify it to your executives. It’s a challenge to document where you will get that value back. As I talk with IT leaders at different conferences and forums, that’s the number-one thing I hear: They just can’t come up with the value case to move to SAP S/4HANA in the short term.
Ann Marie: If your SAP ECC system is running perfectly, why would you make the effort to change it?
Chris: That’s right. One of the things I explained to our leadership team is that a lot of companies are moving to SAP S/4HANA to consolidate the finance pieces from several ERP systems. When you’re already on a single instance like we are, there’s not as much value in just upgrading the core as there is when you can consolidate several different ERP systems into one.
Ann Marie: Very true. You touched on data as one of the benefits of having a single global ERP. Data management comes up all the time as a huge pain point across all industries, chemicals included. How do you approach enterprise-level data management at Dow?
Chris: This is a great question, and it’s one of the biggest topics at Dow. We do have one global data warehouse and one ERP system. Employees can use our centralized business warehouse, and we’ve also put good practices in place for employees to use advanced analytics tools to display that data in better ways. When it comes to reporting global financial and order data, we’re in a really good position.
We also put a centralized group in place about five years ago that manages a few of the most critical enterprise data objects in the company—specifically customer, vendor, and material. The businesses and functions at Dow create those data objects, but the centralized group owns the process and shepherds the requests through the creation process to make sure we have consistency and some level of speed.
Ann Marie: How do you make sure that your data is accurate, timely, and accessible across the business?
Chris: About a year ago, we created an information quality team that is now working with our business units and our functions to bring more visibility to data quality and data integrity for all of the objects across the landscape—even transactional data. That’s a big move forward for us, but it is proving to be valuable. One big thing we’re finding that as we try to support our digital presence with our customers—for example online ordering like I talked about earlier—the biggest barrier to doing that is data quality.
As we’re running those projects, this information quality team is a partner helping with the analytics to find where we need to focus on cleaning up the data. But even with all of that in place, data integrity continues to be a focus and a challenge as it is with all large companies. One of the challenges you run into is everyone talks about what a challenge and an issue it is, but it’s always one of those things that seems easy enough to put on the back burner at times. What we’re trying to do is heighten why it’s so important to focus on this, especially as we get more digital with our customers or open up more of our data to them. That data has to be clean.
Ann Marie: The ownership issue is tough, too. Everyone needs data and touches it, but who really owns it? Is your information quality team cross-functional?
Chris: It is a small team that sits in information systems on the IT team, but its members partner with different areas of the business. They bring us best practices in data visualizations and data mining that we can use across our businesses and functions.
Ann Marie: So, they’re acting a little bit like a center of excellence?
Chris: That’s a good way to think of it. At the end of the day, though, we can’t have IT “owning” the data for the company—that needs to sit with our business units and various functions in the company as a partnership. We will have a large focus on data governance and management as we move forward with our digital journey.
Ann Marie: Thank you for sharing what you’re working on with your team at Dow, Chris.
Have you upgraded your supply chain technology stack, navigated an SAP S/4HANA migration, or solved an operational business challenge through technology or process improvements? Your peers are eager to learn from your experience at the upcoming ASUG Best Practices: SAP for Supply Chain virtual conference on May 11-12, 2021. Submit your presentation abstract for an opportunity to share your SAP journey.