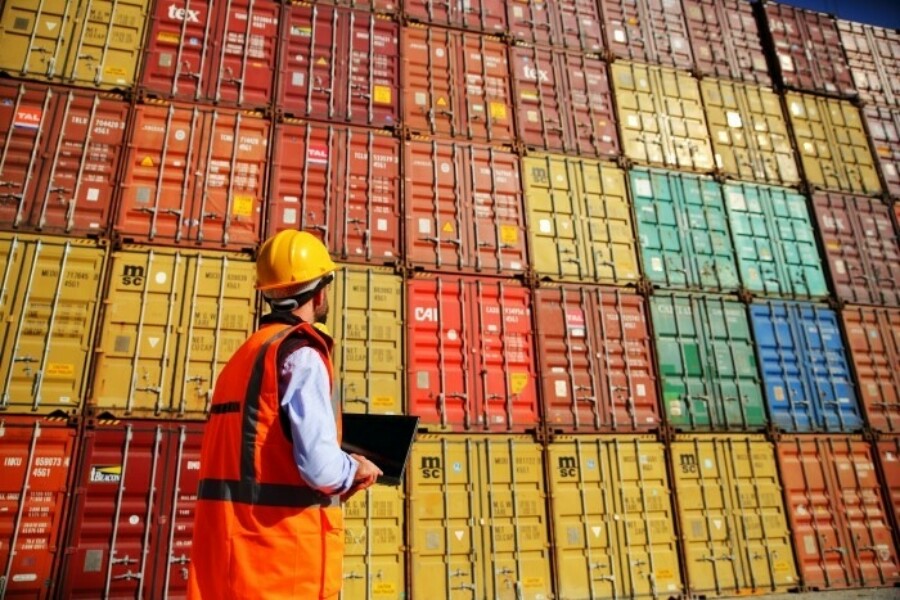
Over the past year, the world has watched as COVID-19 has shuttered restaurants and bars, forced non-essential workers and students into quarantine, and lay siege to the health care industry. The outbreak is having a profound impact on industries and institutions that are integral to modern life. Of all of our modern institutions, one of the systems most affected by COVID-19 is the global, just-in-time supply chain businesses of all types have come to rely on.
These established lines of trade control not only what we can purchase as consumers, but also what manufacturers of all types and sizes can produce in the first place. All over the world, difficulties posed by COVID-19 are disrupting the supply chains we depend on for food, medicine, cleaning supplies, and, of course, toilet paper.
The Biggest Supply Chain Disruption Since WWII
“The level of disruption in a short space of time has been monumental,” said Richard Sandall, chief supply chain evangelist at Innovapptive, a mobile supply chain and plant maintenance solution provider and SAP partner. “COVID-19 is probably the biggest disruption to supply chains that we’ve seen since World War II. It’s affecting the entire globe.”
What makes the impact of COVID-19 so remarkable is how it is affecting every aspect of the supply chain, complicating both upstream and downstream supply lines. Companies are having trouble acquiring the materials needed to make products, and they are struggling to ship their products to stores and wholesalers. Unlike other disruptions, COVID-19 is impacting virtually every single aspect of supply chains.
Short-Term Effects of COVID-19 on Supply Chains
As COVID-19 forces the closures of production plants and businesses, the sheer effect of those closures is weighing heavily on current supply chains through disruption and demand imbalances.
“Our international supply chains are fraying and breaking down,” said Tom Craig, CEO of Tom Craig Consulting. Craig spoke about the Port of Virginia, which announced that it will soon close its cargo terminal because of a drop in the volume of products and resources moving through the port.
“There are so many container ships laid up because there is no cargo for them,” Craig said. “I think that will continue for a while until the economy demand shock passes.”
Another prominent example is the American automotive industry, which came to a halt when production plants closed down as a way to curb the spread of the disease. Some automotive suppliers even pivoted their factories from making cars to building ventilators. As the industry looks to restart, Sandall said companies are taking measures in plants and warehouses to avoid further spread of the virus. These measures include running production lines at slower speeds, assigning workers to designated work areas, and sanitizing equipment between shifts.
Supply Chains After COVID-19
Moving forward, the COVID-19 outbreak will also have some wide-reaching, long-term effects on supply chains. Sandall said that companies have focused on least-cost supply chains over the last two decades. But that will change after COVID-19.
“There’s now going to be a much bigger focus on building resilience, contingency plans, and risk assessment into supply chains,” Sandall said.
Bringing the Supply Chain Back Home
Part of this focus includes reshoring—moving production back into its home country—as opposed to outsourcing or offshoring production. Many American companies will begin examining how to produce their products either back in the U.S. or in a closer location. This process could take some time, however, as the U.S. has a sizeable (but shrinking) international trade deficit and imports billions of dollars of goods each year.
“It took us decades to get where we are,” Craig said. “This change isn’t going to happen overnight.”
Planning Around Potential Supply Bottlenecks
The COVID-19 outbreak also is encouraging companies to re-examine the supply chain best practices and contingency plans they have in place.
“This outbreak shines a light on the need for true business continuity and disaster recovery planning,” said Chris Haydon, president of SAP procurement solutions. “It’s pretty clear this is an area that wasn’t ready.”
According to Haydon, companies will begin analyzing and understanding key bottlenecks in their supply chains. Most importantly, the outbreak allows companies to evaluate supply-chain risks. “This is how companies will get stronger,” Haydon said. “They’ll be able to go back and examine the supply chain capabilities of their core business processes.”
As companies figure out how to conduct business in this environment, they also need to make sure that what they rebuild is sustainable. “You now have to be responsive and see what's coming at a different rate,” Haydon said. “You can take nothing for granted.”
ASUG is continuing the supply chain conversation with its upcoming virtual event, ASUG Best Practices: SAP for Supply Chain. On May 11 and 12, hear from customers, experts, and thought leaders on how the last year has challenged and changed supply chains, and what technologies companies are using to bolster their supply chains.