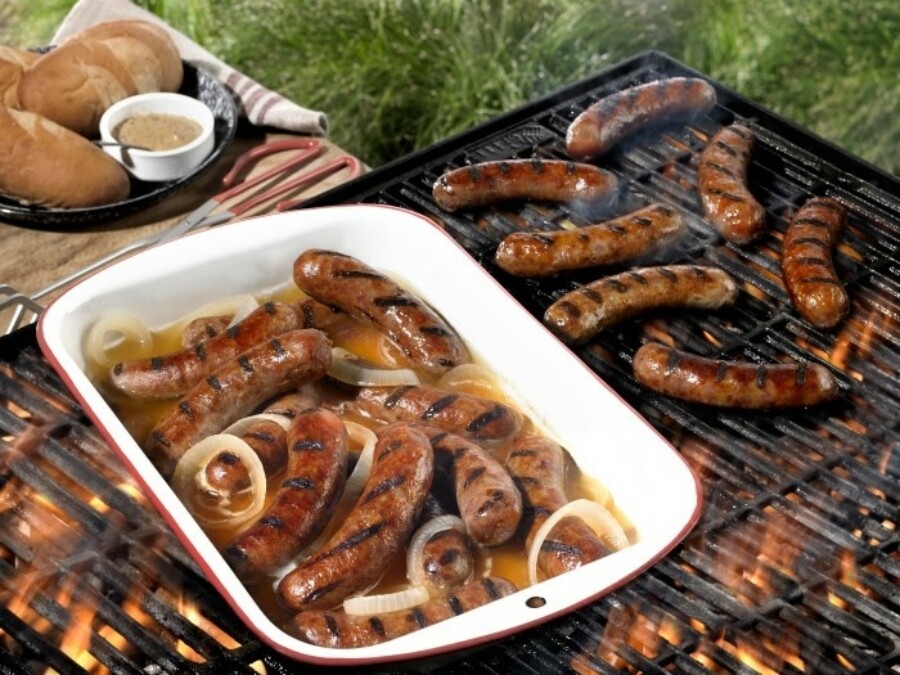
Johnsonville, LLC—one of the most popular sausage brands in the U.S.—had a solid SAP ERP system in place. But the team lacked a way to use this technology to schedule routine and unexpected maintenance.
To fill this gap, Bob Meyers, Johnsonville’s business partner for operations, supply chain, and engineering, and Chad Pennings, the company’s maintenance and reliability analyst, were tapped to implement a new technology solution and introduce it across Johnsonville’s facilities.
Both men talked with ASUG News about the system they designed to manage the maintenance the company needs to keep production lines running smoothly. As a result of collaborating with teams across Johnsonville, they developed and launched a system that makes the best use of their maintenance staff at the right times.
Ann Marie: What’s your plant environment like at Johnsonville? How many people are on your service team, and what are they responsible for maintaining?
Chad: We focus on making raw and ready-to-eat meat products. Our manufacturing facilities require a high wash-down environment. That means we have to tear almost every piece of equipment all the way down to the frame daily, wash it with high pressure hot water at 180 degrees, and then put it back together for the following production shift. It’s a labor-intensive environment.
Across our facilities, we have about 160 maintenance technicians, including maintenance planners, inventory team members, maintenance coordinators, utilities technicians, refrigeration technicians, and junior techs. We’re responsible for maintaining everything from the building to 100 percent of our equipment assets.
Ann Marie: What were some of the challenges that inspired your work planning, scheduling, and prioritization project?
Chad: The biggest challenge was prioritizing work correctly. We saw opportunities for corrective maintenance and predictive processes, and we believed we could also make repairs more quickly through a robust prioritization process. If not addressed in a timely manner, these situations could turn into emergency work orders, leading to additional downtime during production.
We also were not using our staff-member resources to their fullest capacity. We were scheduling members lightly when they had extra time available and at other times overloading them when they were already at capacity for the day. There have also been times when we’ve scheduled members to work when they were on paid time off.
Ann Marie: What were some of the ripple effects of these production slowdowns?
Chad: The biggest impact was when these slowdowns pushed our planned production needs out into the weekend, creating overtime for our members. When we push our production into the weekend, that not only increases our labor costs, but also takes time away from important corrective and preventative maintenance work.
Ann Marie: How did you start scoping out the needs for this project?
Bob: We started by identifying from the organization’s perspective what we wanted to accomplish during the project. Then we asked five companies to tell us how their systems and software would meet our needs.
Chad: We formed a project team that included maintenance coordinators and planners, global maintenance members, IT support, and a few facility team leaders to help us map out our desired future state.
Ann Marie: How did you determine who would participate in the project? And how did you address the needs of folks who were not on the project team?
Bob: We added to the expertise on the project team. After the first or second week we discovered that we also needed to bring some of our maintenance team leaders on board. We expected the maintenance members to keep their coworkers at their facility informed about what we were doing. The team leaders brought feedback from the facility to us every week, which is how we bridged the gap.
It worked really well. Obviously, some members had more concerns than others. We had to meet with some folks one-on-one to talk through the processes. But some of them had legitimate concerns that changed the scope of the project for the better. Communication takes time, but it is time well spent.
Ann Marie: How did you ultimately define your processes and then design your system to prioritize the work?
Chad: We already had good SAP maintenance processes in place with well-defined workflows, but we needed to understand how Viziya, the new tool we selected, would fit into our current processes to determine the scope of changes needed. The project team and maintenance teams determined our final processes.
We modified Viziya’s standard blueprinting process. Our team members are more hands-on than most. Instead of developing a detailed blueprint, we got our hands in the system to learn its capabilities from the beginning of the project. This allowed our planners to be better troubleshooters of the software, take more ownership of the new processes, become subject matter experts for their facilities, and ultimately better understand how SAP and Viziya work together.
Here’s how we prioritized work: After we defined the processes and went through them with the team, we sat down with our planners and team leaders. We did a whiteboard design of how we would prioritize work orders using the different coding fields in SAP that we use today. Then, we did the programming and validated the accuracy of the prioritization with our production leadership and maintenance leadership teams.
We went to all the plants and talked with each leadership team to gain their support on the new prioritization process. This process is now standard across the entire organization.
Ann Marie: How does your system decide how to assign the right work to the right job?
Chad: Two ways. One is that we have team members assigned to work centers. For example, we have work centers specifically for refrigeration, maintenance, machine operators, and controls. Each work center has its own “bucket” of work assigned to it.
The other way we do it is through our technicians’ planner knowledge and their capabilities. We use our newly created weighting system to prioritize work from the most critical to the least critical items.
Ann Marie: What role does technology play in helping you prioritize the work? You mentioned that you have some predictive maintenance capabilities.
Chad: Our Ignition (Industrial Internet of Things) system provides us with downtime for specific pieces of equipment. From those downtime events (DT) we create corrective action work orders (WO) in SAP. These work orders are coded within SAP based on “Maint., Activity Type, Criticality, etc.” We also use predictive tools, such as ultrasound and oil analysis, to help us prioritize work. We have different codes in SAP for how we rank that work and its importance.
Ann Marie: What visibility over the system do you have now that you didn’t have before?
Chad: Viziya has provided us better visibility of members’ schedules. The ability to code work orders as “running” versus “non-running” allows for weighting of work orders, visibility to equipment use, and faster scheduling of work orders than before. We also have visibility to new scheduling key performance indicators (KPIs) that we didn’t have before.
Ann Marie: Did you encounter any change management issues during the process? If so, how did you address them?
Bob: In every project, you will have change management issues. We had weekly meetings not only with our core team but with the plant coordinators. We spent three weeks training our team members and tried to keep them informed of what we were doing.
Chad: We quickly realized that the new scheduling process would affect all maintenance technicians. We developed detailed work instructions and training as part of the project, along with a communication plan that made sure all affected members were kept informed of the project’s progress and changes.
Ann Marie: What’s on your road map to tackle next?
Chad: Our internal IT department is always working on small enhancements and continuous improvements in SAP. We might tackle a mobile solution in the next couple years. We know that could increase efficiency within our current maintenance processes.
Bob: Getting data from our equipment into our SAP ERP or SAP BusinessObjects so that we can write reports and continue to prioritize well will have a huge impact.
Ann Marie: Thanks, Bob and Chad. I really appreciate you sharing your story with us.
Join us in San Antonio on March 16–18, 2020 at SAP-Centric EAM to hear how your peers are solving similar challenges at their own plants.