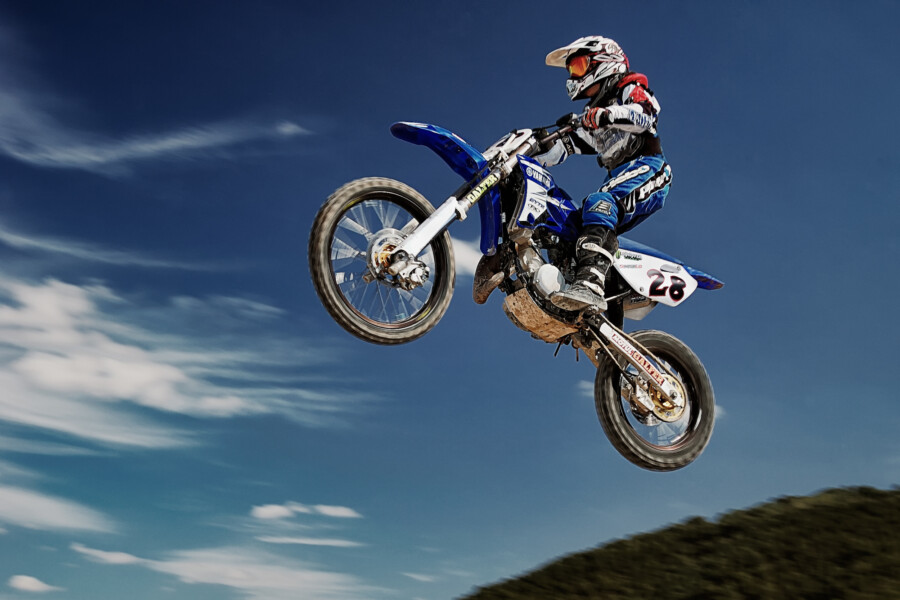
A leader in designing and manufacturing products such as motorcycles, off-road vehicles, automobile engines, and more for over 50 years, Yamaha Motor Corporation USA recently found itself at a crossroads.
Between the rapid evolution of electric vehicles and the advent of digital technologies reshaping its industry, the company knew it needed to adapt traditional systems and frameworks to remain competitive and fuel future innovation.
With that objective in mind, business leaders launched Yamaha’s Next Phase, a global initiative aimed at transforming the way the company operates.
One of the first steps in this journey involved documenting business processes across the organization; in doing so, Yamaha quickly discovered that more than simply mapping process flows was required to drive lasting change. Business leaders needed a solution that would help them identify improvement opportunities, plan enhancements, and effectively communicate these changes to stakeholders throughout the organization.
Enter SAP Signavio, the core of SAP’s software suite for business process management.
“It was a real ‘wow’ moment when we first saw SAP Signavio solutions,” recalled Chuck Bohannon, senior manager of SAP and parts/accessories at Yamaha Motor Corporation, USA, in an ASUG interview. “We immediately felt they would add a significant amount of value, not just for individual processes in key business areas but for the organization as a whole. I wish we’d had these solutions sooner.”
Shifting Gears: Overcoming Challenges and Setting the Right Foundation
Before implementing Signavio, Yamaha faced several obstacles that hindered its ability to drive process improvements effectively. The lack of process visibility across the organization led to communication breakdowns between departments, with different teams using varying process flows to achieve the same goals — a roadblock that made it challenging to identify and implement necessary improvements.
Yamaha’s journey with Signavio began with the SAP Signavio Process Manager solution. Initially viewing the tool as “Visio on steroids,” the company realized Signavio offered much more than mere process mapping after a deeper exploration of its capabilities.
Leaders learned early on the importance of starting with a clear strategy and approach. “If we had it to do ever again, we would have started with a plug-and-play approach, much more so than our beginning point, which was basically Visio diagrams inside Signavio,” noted Bohannon.
“The first step you take is always the most important.”
Paul Mears, manager of SAP OTC applications at Yamaha, echoed this sentiment: “The first step you take is always the most important. We would definitely start with process mining and plug-and-play.”
The company realized it was crucial to familiarize themselves with business process model and notation (BPMN) standards and implement an organizational strategy before creating hundreds of diagrams. By failing fast and gaining insights from the experience, leaders learned to refine their approach and began to gain traction with Signavio.
Throttling Up: Powerful Features and Tangible Benefits
As Yamaha made headway in its SAP Signavio implementation, managers uncovered the value of various features within the solution.
Process simulation, for instance, allowed Yamaha to model an as-is process, assign dollar values to tasks, and then create a new revision with automation applied. This capability helped build a compelling business case for leveraging robotic process automation, demonstrating the potential efficiency gains and cost savings.
Meanwhile, features like the reusable data dictionary elements and object attributes, collaboration hub, process governance, and reporting capabilities proved useful. SAP LeanIX connectivity was a significant benefit that allowed Yamaha to maintain a single source of truth for its business applications.
The impact of SAP Signavio was not just qualitative but also quantitative. Yamaha anticipates a 25% value addition to key processes through improvement actions and a 15-20% annual recurring business benefit in cost savings and efficiency.
Signavio’s impact went beyond process optimization, playing a vital role in empowering Yamaha’s workforce and cultivating a mindset of ongoing improvement.
By formalizing an organization-wide effort to document business processes, team members gained visibility and accessibility of process information for all employees, which enhanced training and onboarding of new staff, as well as increased collaboration and communication between business and IT teams.
“Any given business person, security person, or key person can go into Signavio, and they’ll know exactly what security a stakeholder needs, what roles they are going to play, and what processes they will be involved with,” said Bohannon, discussing how the solution enabled Yamaha’s employees to work more efficiently and effectively. “They’ll have visibility to all of that.”
Despite Yamaha’s expanding knowledge and utilization of SAP Signavio, the value of other integrations became evident, leading the company to leverage SAP Solution Manager and SAP LeanIX to streamline its process management efforts.
“It’s going to be a fantastic tool, but you need some expertise to fully understand what you’re getting out of it.”
Having a fresh understanding that any digital transformation initiative is not without its challenges, leaders were prepared to overcome whatever obstacles lay ahead. “We came into LeanIX much like we came into Signavio,” explained Bohannon. “It’s going to be a fantastic tool, but you need some expertise to understand what you’re getting out of it fully.”
Mears emphasized the importance of having an enterprise architecture design and understanding the links between tools. “Having a general mud map [diagram] of what you want to achieve and the timelines around it, rather than implementing on the fly,” will help teams stay focused and avoid backtracking, he noted. “It’s beyond important to know how they all connect and what that’s going to look like before you jump too far down the path,” added Bohannon.
Accelerating Digital Transformation
Ultimately, Yamaha found SAP Signavio’s integration capabilities to be a game-changer.
With a successful implementation of SAP Signavio under its belt, Yamaha is now looking toward the future. The company plans to implement the SAP Signavio Process Intelligence solution and further integrate LeanIX to propel its business transformation forward.
Furthermore, Yamaha is preparing for its global SAP S/4HANA rollout, with the first go-live scheduled for February next year. The undertaking is as far-reaching and multifaceted as the company’s diversified portfolio and geographical footprint.
“We’ve got 12 waves of this S/4 rollout, and that’s primarily just here in North America,” said Bohannon. “But then quickly following that will be our golf cart division, other affiliates, propeller company, and some of our boat builders. We’ve got a host of continuations within our regional rollout model.”
Although this process is ongoing, Yamaha’s journey with SAP Signavio underscores not only the value of the solution but also the importance of embracing change and uncovering new ways to drive growth and optimization.
The company anticipates that SAP Signavio’s integration capabilities with tools like Tricentis and SAP Enable Now will facilitate more effective and efficient process enhancement activities, fostering better alignment between business leads and IT.
“We want to use the collaboration hub as a one-stop-shop for people to view and understand our processes,” explained Mears. “To have that, we need to have a very fluid transition from workstream to workstream.” By running workshops with different workstreams and exposing people to these concepts, Yamaha is making progress in building the necessary skill sets and awareness to support their transformation efforts.
Another critical aspect of Yamaha’s future-focused approach is leveraging such tools to keep training documentation up-to-date and in sync with the latest processes. As Bohannon pointed out, “As soon as training documentation gets written for an application, it’s basically obsolete because something will have changed within the next day.” By integrating Signavio with Enable Now, the company can ensure that new hires are onboarded with the most current information, making the training materials “perpetual documents and always in sync.”
Reflecting on the journey thus far, both Bohannon and Mears expressed satisfaction with the progress made and lessons learned along the way. “We have no regrets whatsoever because it’s gotten us to where we are today,” concluded Bohannon. “I will tell you, we’ve learned a significant amount over the last year and a half.”
Crossing the Finish Line: Takeaways and Continued Innovation
Yamaha’s journey with SAP Signavio highlights several takeaways for organizations embarking on their own business transformation initiatives:
- Start with a clear strategy and approach, focusing on process mining and plug-and-play solutions.
- Familiarize yourself with industry standards and best practices to ensure a solid foundation.
- Embrace a holistic approach to transformation, considering the integration of multiple tools and systems.
- Empower your workforce by improving process visibility, accessibility, and collaboration.
- Learn from experiences and adapt your approach along the way.
As Yamaha Motor continues to drive innovation and growth, its utilization of SAP Signavio will play a role in navigating future challenges and opportunities. With a strong foundation in place and a commitment to ongoing improvement, Yamaha is well-equipped to scale its transformation efforts and maintain its position as a leader in the industry.
For businesses looking to drive their own transformations, Yamaha’s success story serves as an inspiration. By leveraging the power of SAP Signavio and embracing a culture of ongoing improvement, companies can modernize operations and achieve new levels of efficiency, agility, and innovation.