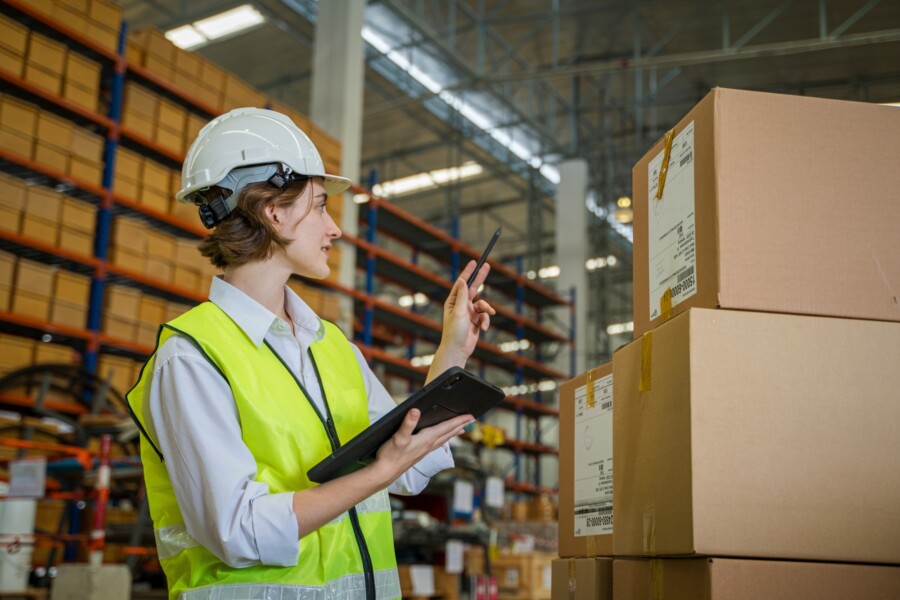
From materials planning to procurement and inventory, many areas of focus for organizations require a mastery of business processes and configuration related to materials management with SAP S/4HANA.
That’s why Jawad Akhtar, an SAP logistics and supply chain management expert, and Martin Murray, a respected logistics consultant and 15-year veteran of IBM, initially teamed to author Materials Management with SAP S/4HANA, a definitive guide to configuring and managing these vital business processes in SAP S/4HANA.
In their SAP Press publication, recently updated and revised for its third edition, Akhtar and Murray walk readers through creating organizational structure and defining business partners and material master data, also offering step-by-step instructions for essential processes like purchasing, MRP runs, and goods issue and receipt.
More overarchingly, the authors provide their readers with an understanding of how to get the most out of their investment in SAP S/4HANA as it relates to procurement and planning, inventory management, and more advanced processes (such as batch management, demand-driven replenishment, SAP Document Management System (DMS), and new SAP Fiori apps for reporting and monitoring).
Below, Akhtar took the time to outline six essential steps for materials management with SAP S/4HANA:
1. Implement flexible workflows for a more streamlined and timely approval process (Chapter 8)
The flexible workflow tool in SAP S/4HANA facilitates the approval process of procurement elements, such as purchase requisitions, purchase orders, request for quotations (RFQs), quantity and value contracts, scheduling agreements, and service entry sheets. Flexible workflow can be independently set up by a user by bringing together the concepts of release procedures with SAP Business Workflow. A release procedure is an approval mechanism by which a procurement element is approved. However, only one approval or release option can be used at a time, either a standard release procedure or a flexible workflow.
2. Leverage supplier evaluation features for effective supplier relationship management (Chapter 10)
Supplier evaluations facilitate procurement and quality management (QM) functions to pursue business objectives by providing clear and comprehensible key figures. These objectives include the following:
- Determining the current status of a supply relationship
- Determining and communicating the extent to which the requirements of the purchaser are met by a supplier
- Creating a basis for supplier selection or supplier exclusion
- Determining support after an RFQ to extend the supply relationship
- Determining support for higher weighting for goods receipt inspection and inspection planning
Supplier evaluation generally occupies an intermediate position between the procurement subcomponent of materials management and quality management (QM) by incorporating information and criteria from both a commercial and a quality point of view.
During an SAP S/4HANA system implementation project, both procurement and quality teams should deliberate and agree on the percentages and weighting of the criteria and sub criteria that influence supplier evaluation.
3. Implement demand-driven replenishment to reduce the “bullwhip effect” (Chapter 27)
Logistics and supply chain management today have more volatility, uncertainty, complexity, and ambiguity than ever before, making it a no-win battle for a company to manage the chaos that exists between customer demand and the company’s capability for timely supply.
The solution to the distortion of relevant information, and the quagmire of material flows, lies in decoupling the logistics and supply chain to reduce the bullwhip effect. Decoupling refers to disconnecting the ever-present and constantly increasing variability between demand and supply by placing buffers at strategic points, known as decoupling points. Materials planners then regularly monitor the buffers in the material value chain—from procurement to interplant transfer to production to distribution—to ensure timely action and interventions where necessary.
4. Reap tangible business benefits with SAP Fiori analytics apps (Chapter 28)
SAP Fiori is SAP’s next-generation, web-based user experience for working with SAP systems. A large number of SAP Fiori apps are available in SAP S/4HANA, and the apps library is constantly expanding. Apps for master data, transactional data, reporting, and analytics using SAP functionalities are available in the SAP Fiori apps reference library. Due to the highly intuitive nature of apps, you can quickly get up to speed through use.
Let’s discuss two Fiori apps for MM in SAP S/4HANA: the Procurement Overview app, and the Overview Inventory Management app.
- The Procurement Overview app shows the most important information and tasks relevant for procurement personnel. The app displays important information on a set of actionable cards, thereby enabling procurement personnel to focus on the most important tasks, make faster decisions, and take immediate action. The cards show the most important information ranked according to relevance. For example, with the Monitor Purchase Contracts card, a procurement planner sees an instant overview of the consumption and expiry dates for quantity or value contracts.
- The Overview Inventory Management app shows, at a glance, the most important information and tasks relevant for an inventory manager. This information is displayed on a set of actionable cards so that the inventory manager can focus on the most important tasks, enabling faster decision-making and immediate action. These cards show the most important information ranked according to relevance. For example, the Overdue Materials – Goods Receipt Blocked Stock card provides an overview of the overdue materials for which a goods receipt was posted into the non-valuated goods receipt blocked stock.
5. Prevent supply chain disruption with Early Warning System (EWS) for timely alerts (Chapter 26)
The Early Warning System (EWS) is made up of user-defined alerts that are triggered whenever any deviation or exception to an important business process occurs, thus allowing a materials planner to take timely action to minimize disruptions to logistics and supply chains. The Early Warning System (EWS) is built on the same SAP S/4HANA logistics info structures as standard analyses, with the added flexibility for monitoring and receiving alerts for specific exceptions important to business processes.
For example, whenever the stock of a critical raw material falls below a user-defined stock level, the system should immediately alert procurement and production planners through EWS for timely resolution. EWS provides real-time updates and can be tailored to individual needs, and the frequency with which the system should share alerts can be customized. EWS enables business users to define specific alerts to ensure no (or minimal) disruption to logistics and supply chain operations. Not only can the pre-delivered exceptions be changed, but they can also be deleted if no longer needed.
6. Automate logistics and supply chain in the process industry with five batch management features (Chapter 25)
Batch management is an important part of a company’s ability to procure, produce, store, and sell material. The batch defines a quantity of material by characteristics unique to that batch. Those characteristics determine how the material in that batch is used, sold, or moved. Certain materials can be defined in SAP S/4HANA as being “batch-managed.” A batch is a quantity of material that represents a homogeneous unit with unique specifications. The batch of material may refer to a quantity of chemicals that is produced in one process or a quantity of bottles of water that were filled on a certain filling line from a specific tank. Let’s take a brief look at five features of batch-management:
- Batch determination: In a real-world scenario, a warehouse supervisor receives one material in a number of batches, and this will be kept in storage location stock or in warehouse storage bins. When the material needs to be issued to production, a strategy needs to be in place for the system to choose different batches. Defining the strategy in the system by which the system determines and offers the right batch to pick is the process of batch determination. Batch determination can be used in production order, process order, goods movement, sales order/delivery, cost center, and transfer order functions.
- Batch derivation: With batch derivation, a user can efficiently and automatically transfer a batch’s characteristic values from the sender material’s batches to the receiver material’s batches, thereby saving time, data entry effort, and cost. Batch derivation enables a user to maintain one-to-one, one-to-many, and many-to-one relationships between the sender’s and the receiver’s materials for complete visibility of information and data.
- Active ingredient management: Active ingredient management in batch management enables organizations to take advantage of material valuation at the batch level, as well as the potency or active proportion in the overall quantity of material. This functionality is especially helpful when you’re using an active element or ingredient of a material that contains carrier materials, including impurities. If the total physical quantity of a material is a mixture, then the active or potent material within the mixture is known as the active ingredient quantity.
- Recurring Inspection and Expiration Dates: The ability to inspect batch-managed goods—whether procured raw materials or produced semifinished or finished goods—before their expiration dates ensures there will be sufficient time and flexibility for companies to respond to any unforeseen situations. Recurring inspection (also called repeat inspection) at regular intervals allows business users to take advantage of standard functionality. The batches nearing expiration can go through quality control checks of results recording and usage decisions to decide whether they can still be used. This functionality offers time and cost savings by enabling the business to act proactively and thus optimizes the full logistics and supply chain operations of the company.
- Batch Traceability of Work in Process Batches: Batch traceability is a key functionality used not only in the chemical and food industries but also in almost all industries, including process manufacturing. SAP delivers the batch where-used list in the SAP S/4HANA system. This where-used list enables business users to trace the batch from the finished product to the raw material (top down) or from the raw material to the finished product (bottom up). The work in process (WIP) batch is used to maintain batch traceability for a process order when several batches of raw material are consumed, and several batches of a finished product are generated.
Lastly, let’s discuss a critical report available in batch-management: Batch Information Cockpit. In process industries, such as food and pharmaceuticals, traceability of the ingredients or components within a production or procurement process is of paramount importance. Batch traceability across logistics and supply chain processes is also a legal requirement in many industries and good manufacturing practice to maintain in case there is a batch recall. Companies often develop complex custom reports to view and analyze batch traceability when the Batch Information Cockpit can serve the same purpose. With the Batch Information Cockpit, you can perform top-down and bottom-up traceability analysis. With top-down, analysis of a finished good traces all the raw, packaging, and semifinished materials that were used in making the finished product’s batch. With bottom-up, it’s possible to trace the ingredients or raw materials and trace all the finished goods that were made using these ingredients or raw materials’ batches.
For more insights, purchase Materials Management with SAP S/4HANA from the SAP Press store—and with ASUG membership, you can save 15% on your purchase for a limited time with the code 15ASUG.
To learn more about SAP S/4HANA attend the upcoming event hosted by the ASUG S/4HANA(ERP) Community Alliance. Learn more here.